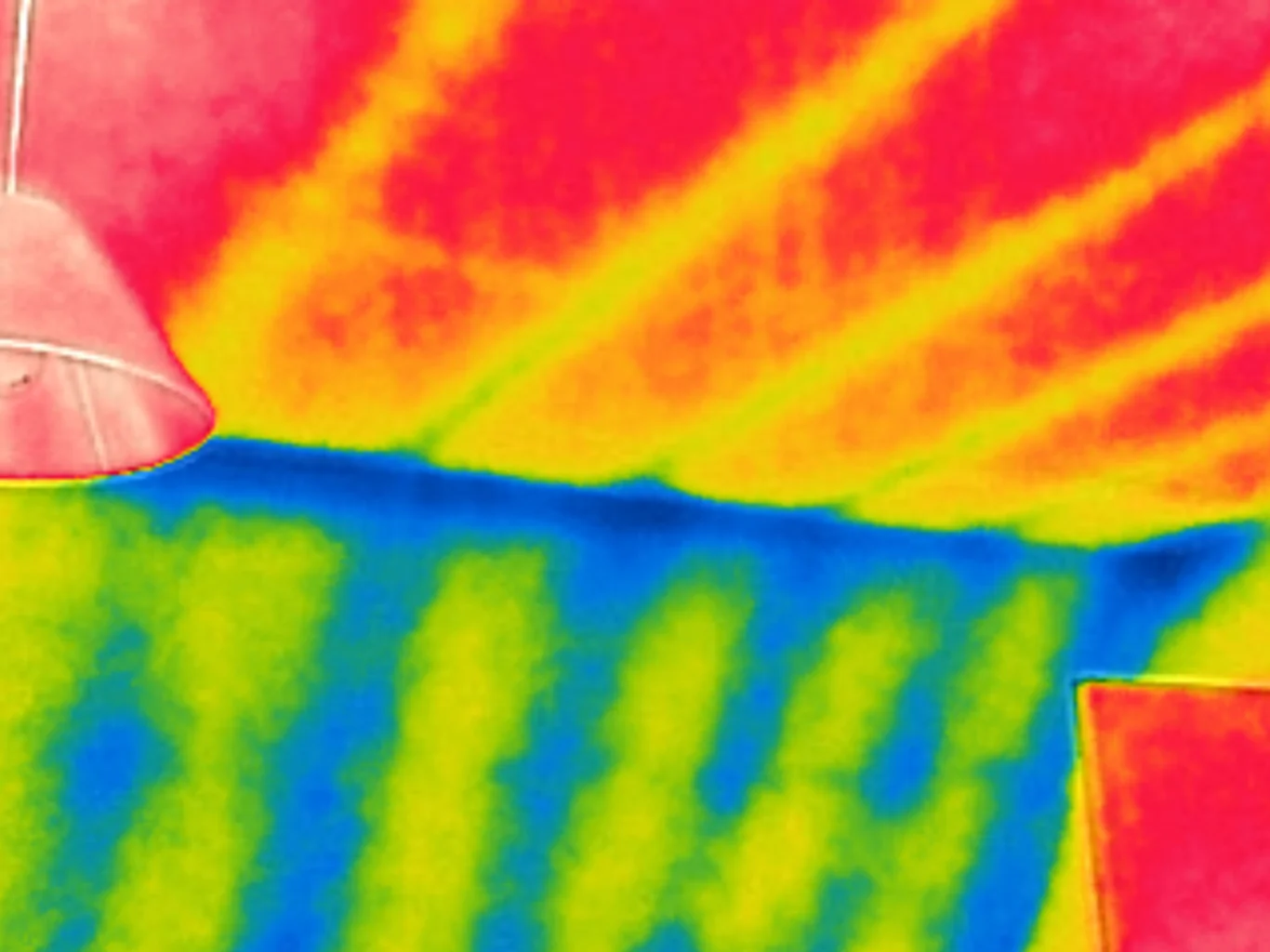
Introduction to Building Thermography: Detecting Non-Visible Defects
Understanding Building Thermography: An Introduction to Detecting Non-Visible Defects
Building thermography is a powerful tool used in the field of construction and maintenance to identify non-visible defects in structures. It involves the use of thermal imaging cameras to capture and analyze the heat patterns emitted by buildings. By detecting variations in temperature, building thermography can reveal hidden issues that are not visible to the naked eye.
This technology has revolutionized the way we inspect and maintain buildings, allowing for early detection of problems and preventing costly repairs.
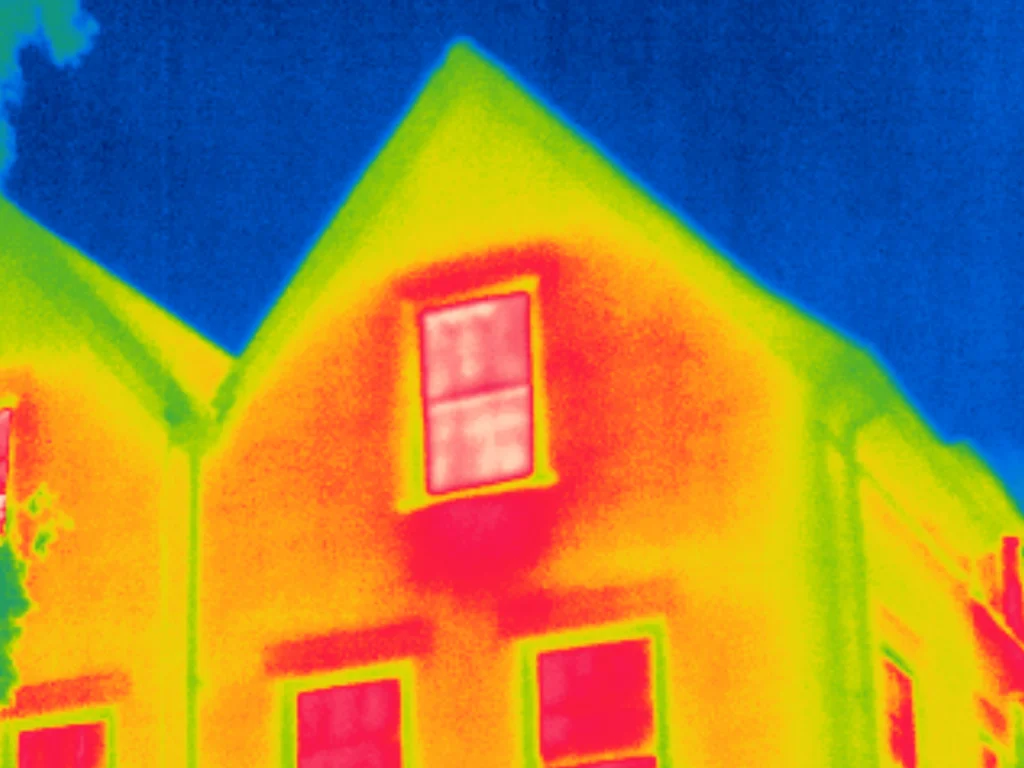
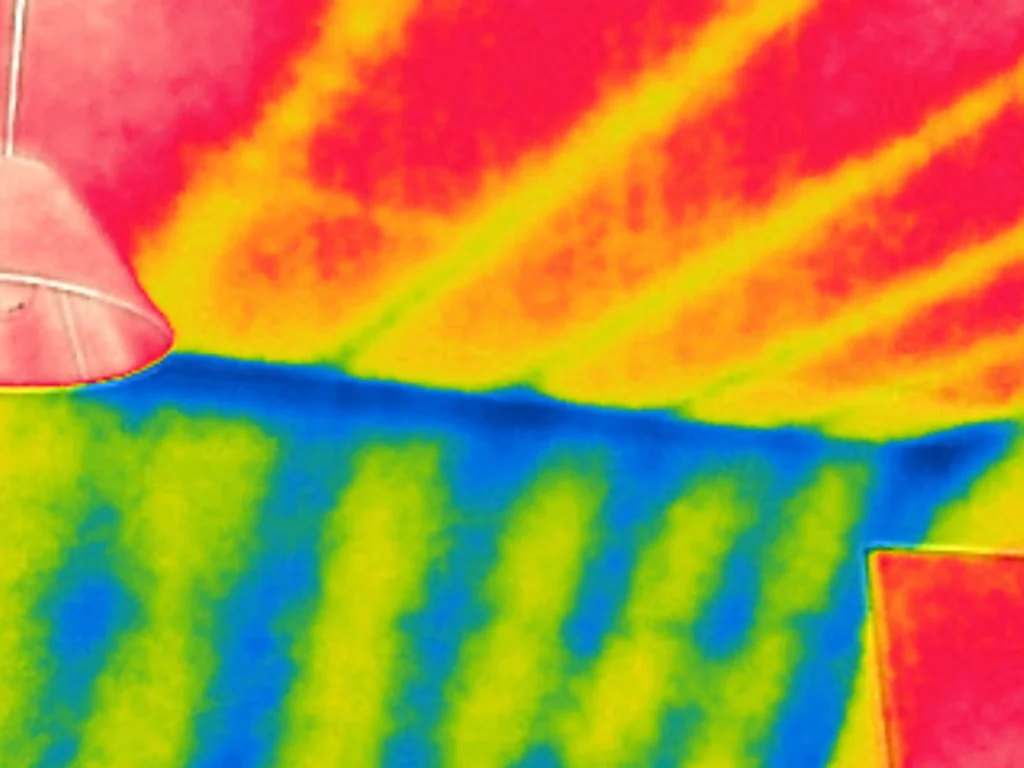
The Science Behind Building Thermography: How it Helps Identify Non-Visible Defects
Building thermography is based on the principle that all objects emit infrared radiation, which is invisible to the human eye. Thermal imaging cameras detect this radiation and convert it into a visible image, where different colors represent different temperatures. By analysing these images, qualified thermographers can identify areas of concern that may indicate non-visible defects in the building.
One of the main applications of building thermography is the detection of insulation issues. Poor insulation can lead to energy loss, resulting in higher heating and cooling costs. By using thermographic cameras, thermographers can identify areas where insulation is lacking or damaged, allowing for targeted repairs and improved energy efficiency.
Another common use of building thermography is the detection of water leaks. Water intrusion can cause significant damage to a building’s structure, leading to mold growth, rot, and deterioration. By using thermal imaging cameras, inspectors can identify areas with abnormal temperature patterns, indicating the presence of moisture and potential water leaks.
Exploring the Applications of Building Thermography: Uncovering Hidden Issues in Structures
Building thermography has a wide range of applications in the construction and maintenance industry. One of its key uses is in the inspection of electrical systems. Overloaded circuits, loose connections, and faulty components can generate excessive heat, which can be detected through thermography. By identifying these issues early on, potential electrical hazards can be mitigated, preventing fires and equipment failures.
In addition to electrical systems, building thermography is also used to inspect HVAC (heating, ventilation, and air conditioning) systems. These systems play a crucial role in maintaining indoor comfort, and any malfunctions can lead to energy waste and discomfort. By using thermography, inspectors can identify issues such as blocked air ducts, malfunctioning components, and air leaks, allowing for targeted repairs and improved system performance.
Furthermore, building thermography is also used in the inspection of roofs. Roof leaks can cause extensive damage to a building’s interior, leading to mold growth, structural deterioration, and costly repairs. By using thermal imaging cameras, inspectors can identify areas with abnormal temperature patterns, indicating potential water intrusion and roof leaks. This allows for timely repairs and the prevention of further damage.
Benefits and Limitations of Building Thermography: Enhancing Inspection and Maintenance Processes
Building thermography offers numerous benefits in the inspection and maintenance of structures. Firstly, it allows for non-destructive testing, meaning that inspections can be carried out without the need for invasive procedures. This reduces the time and cost associated with inspections, while also minimising disruption to building occupants.
Secondly, building thermography enables early detection of defects. By identifying issues before they become visible or cause significant damage, repairs can be carried out promptly, preventing further deterioration and reducing repair costs. This proactive approach to maintenance also extends the lifespan of buildings and improves their overall performance.
However, it is important to note that building thermography also has its limitations. For instance, it relies on temperature differences to detect defects, meaning that it may not be effective in certain situations where temperature differentials are minimal. Additionally, thermography is a qualitative technique, meaning that it can identify areas of concern but does not provide detailed information about the severity or extent of the defect. Therefore, it is often used in conjunction with other inspection methods to obtain a comprehensive understanding of the building’s condition.
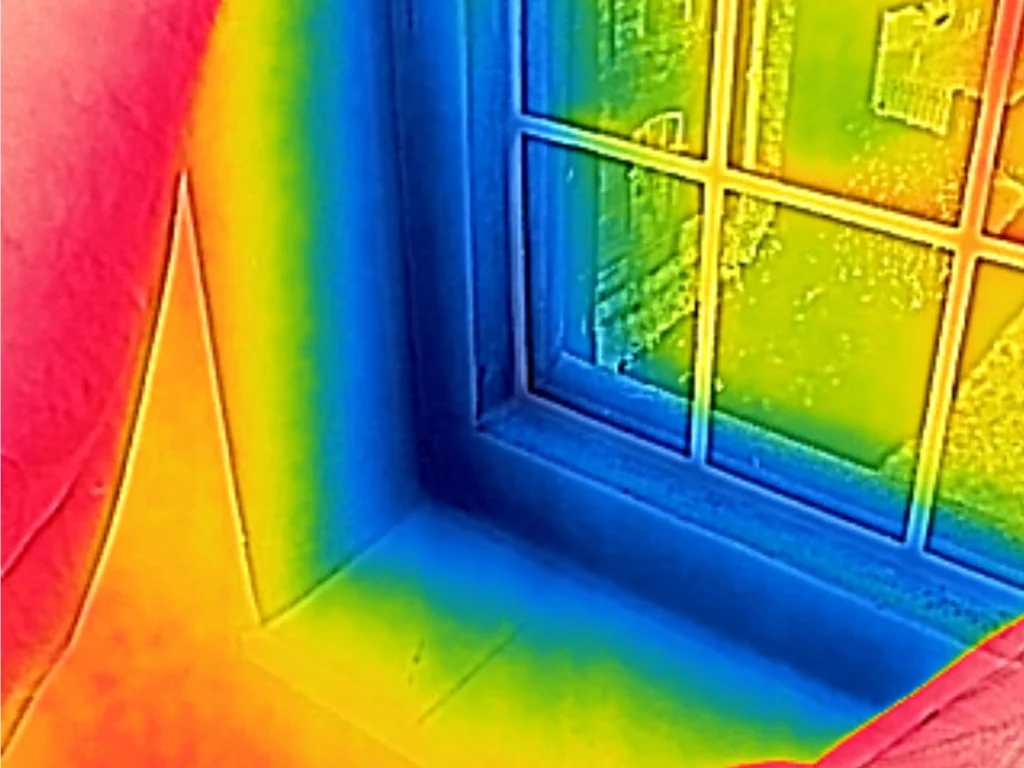
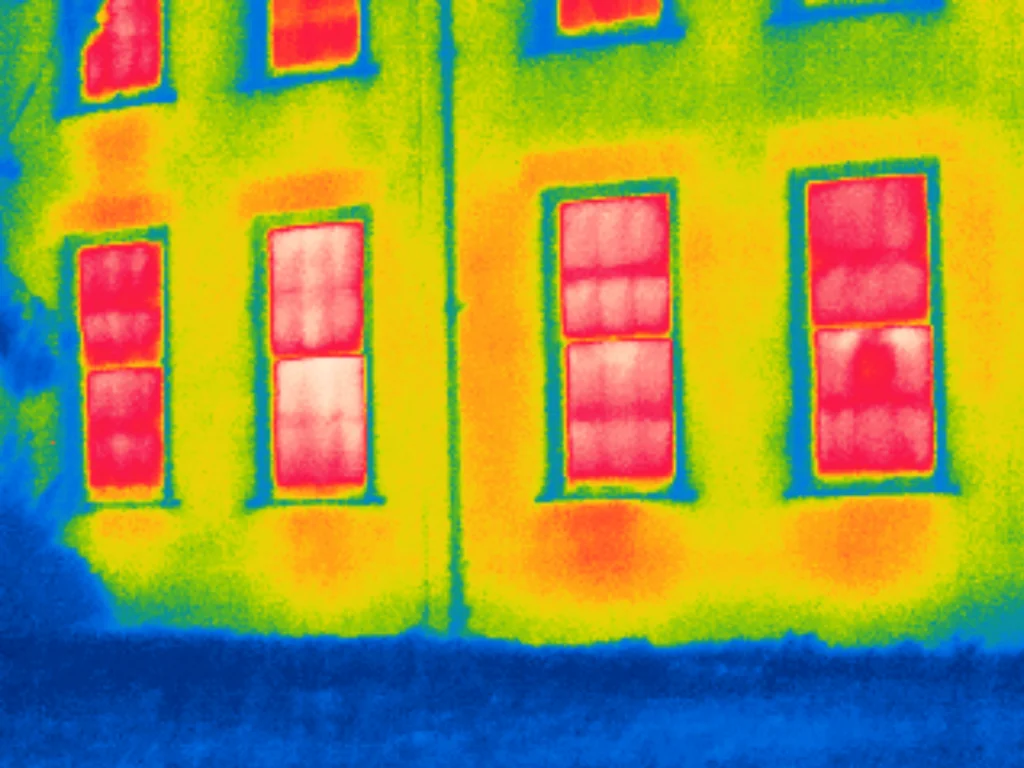
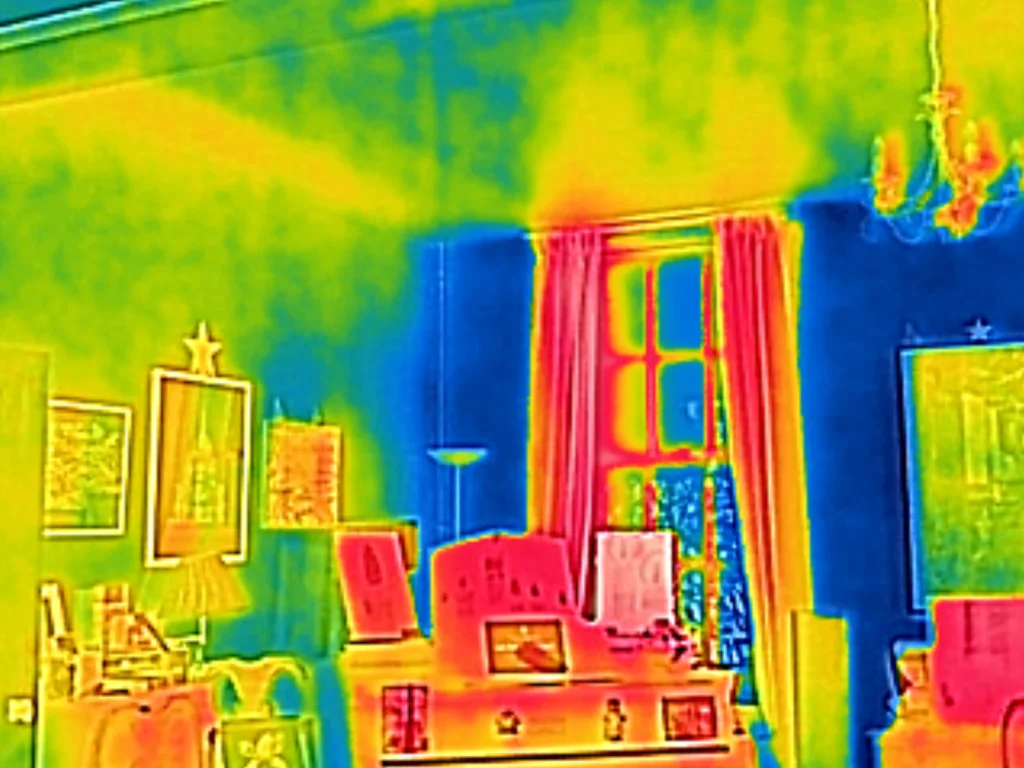
Building thermography is a valuable tool in the field of construction and maintenance. By utilising thermal imaging cameras, inspectors can detect non-visible defects in structures, such as insulation issues, water leaks, electrical problems, and roof damage.
This technology enhances the inspection and maintenance processes by allowing for non-destructive testing, early defect detection, and targeted repairs. While building thermography has its limitations, its benefits far outweigh them, making it an indispensable tool in the industry.
Building Thermography Services
Take control of your building’s energy efficiency and maintenance needs with our Building Thermography Services. Unlock valuable insights into potential energy leaks, insulation deficiencies, and equipment malfunctions. Maximise your savings and ensure a comfortable environment for all occupants. Optimise your building’s performance today. Get in touch for pricing.
Expert Infrared Inspections for Accurate Thermal Assessments
Need professional thermographic analysis for your project? Our certified experts use the latest infrared technology to deliver precise results. Contact Drone Media Imaging today for expert thermal imaging services.
related posts
Pinpointing energy loss in buildings involves identifying hidden insulation defects, thermal bridges, and air leaks. A Level 3 Thermographer employs advanced thermal imaging to ensure precise diagnostics and compliance with energy standards, providing property owners with detailed reports for informed energy efficiency improvements and cost savings.
How To Detect A Faulty Solar Panel.? When faults develop with a solar panel the result is that these cells will heat up. This is because the energy generated by the electrons moving around is not flowing through the panel and onto the convertor, and must manifest somehow, it doesn’t can’t just disappear, so the energy becomes heat.